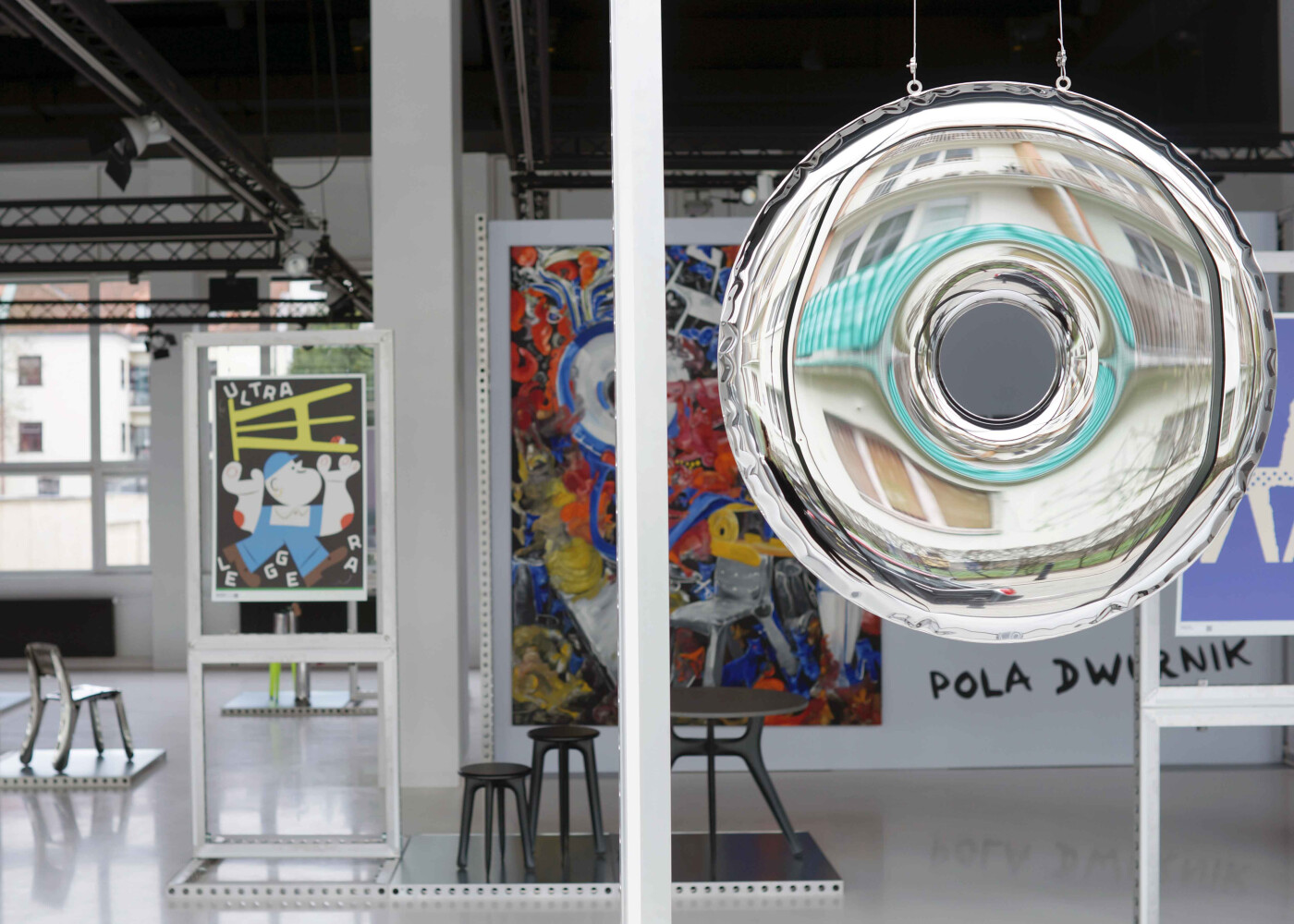
Zieta Studio at Salone del Mobile.Milano 2024


-medium.jpg)
-medium.jpg)
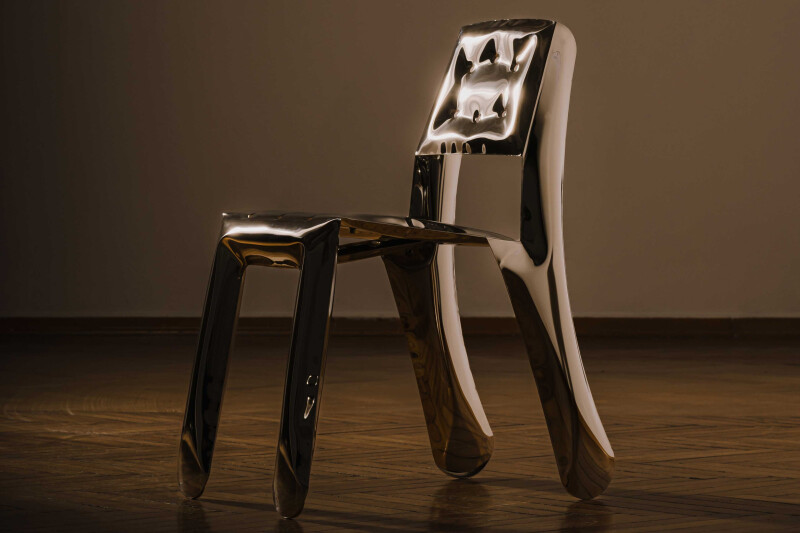


-medium.jpg)
-medium.jpg)


-large.jpg)
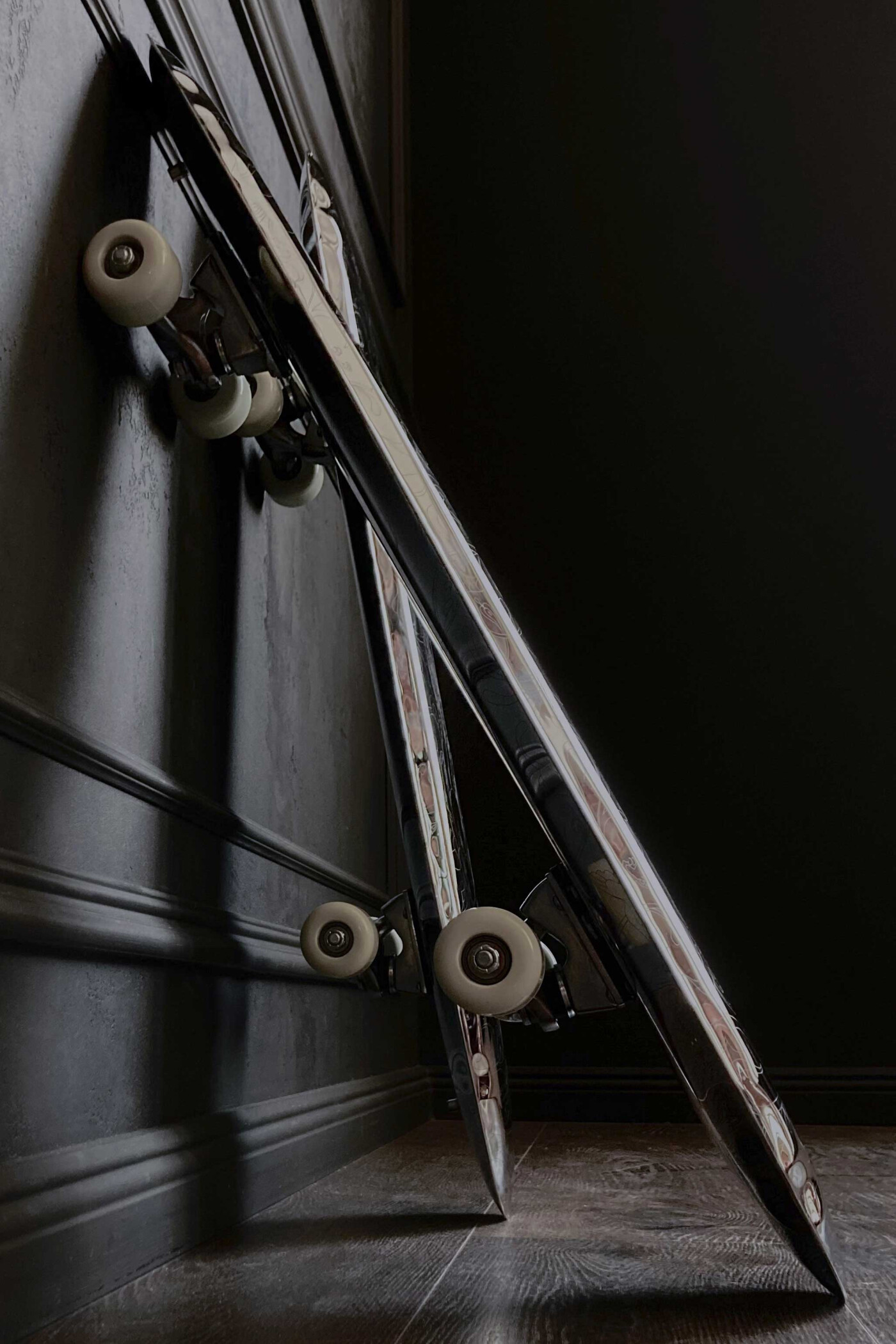


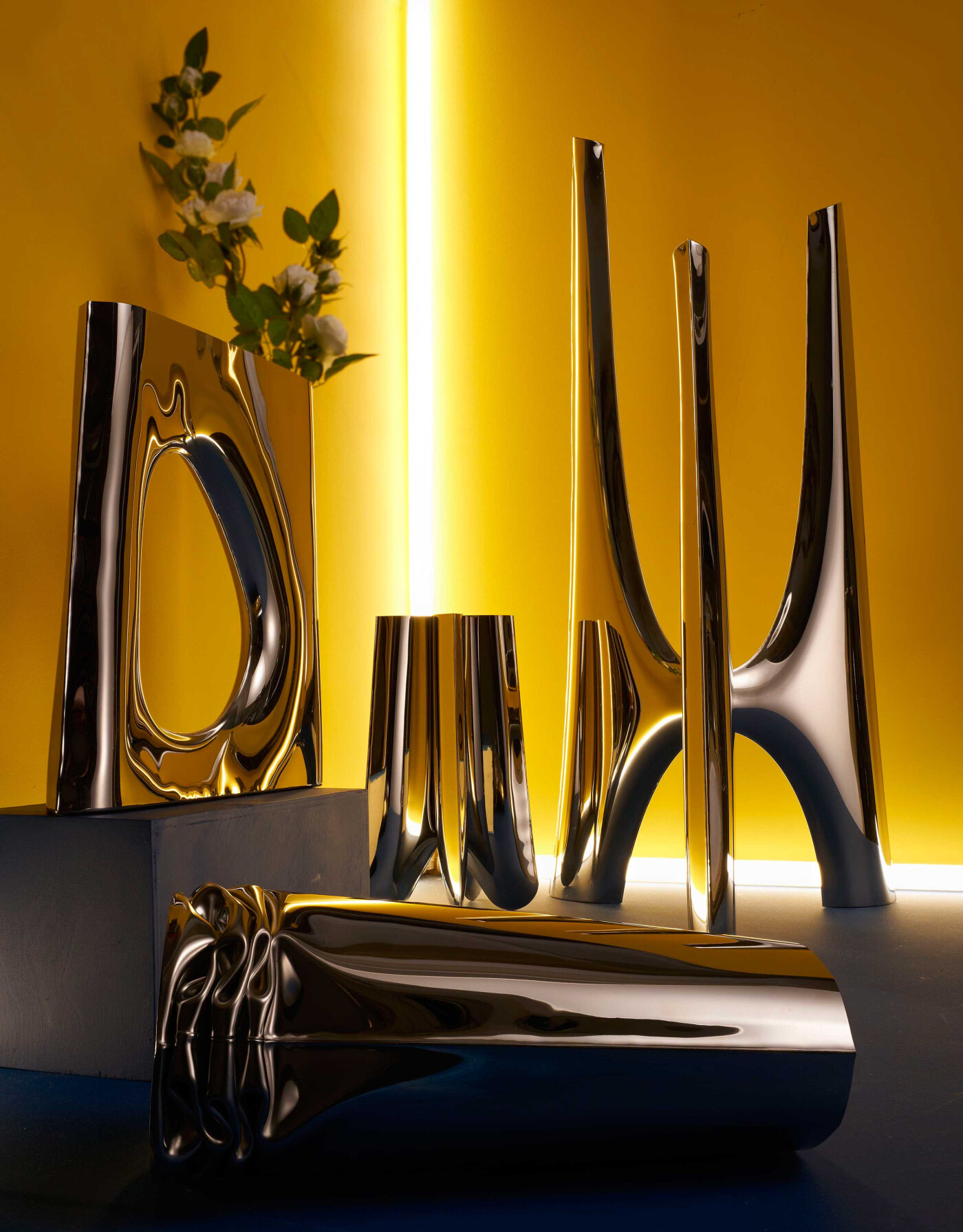
News
What's new
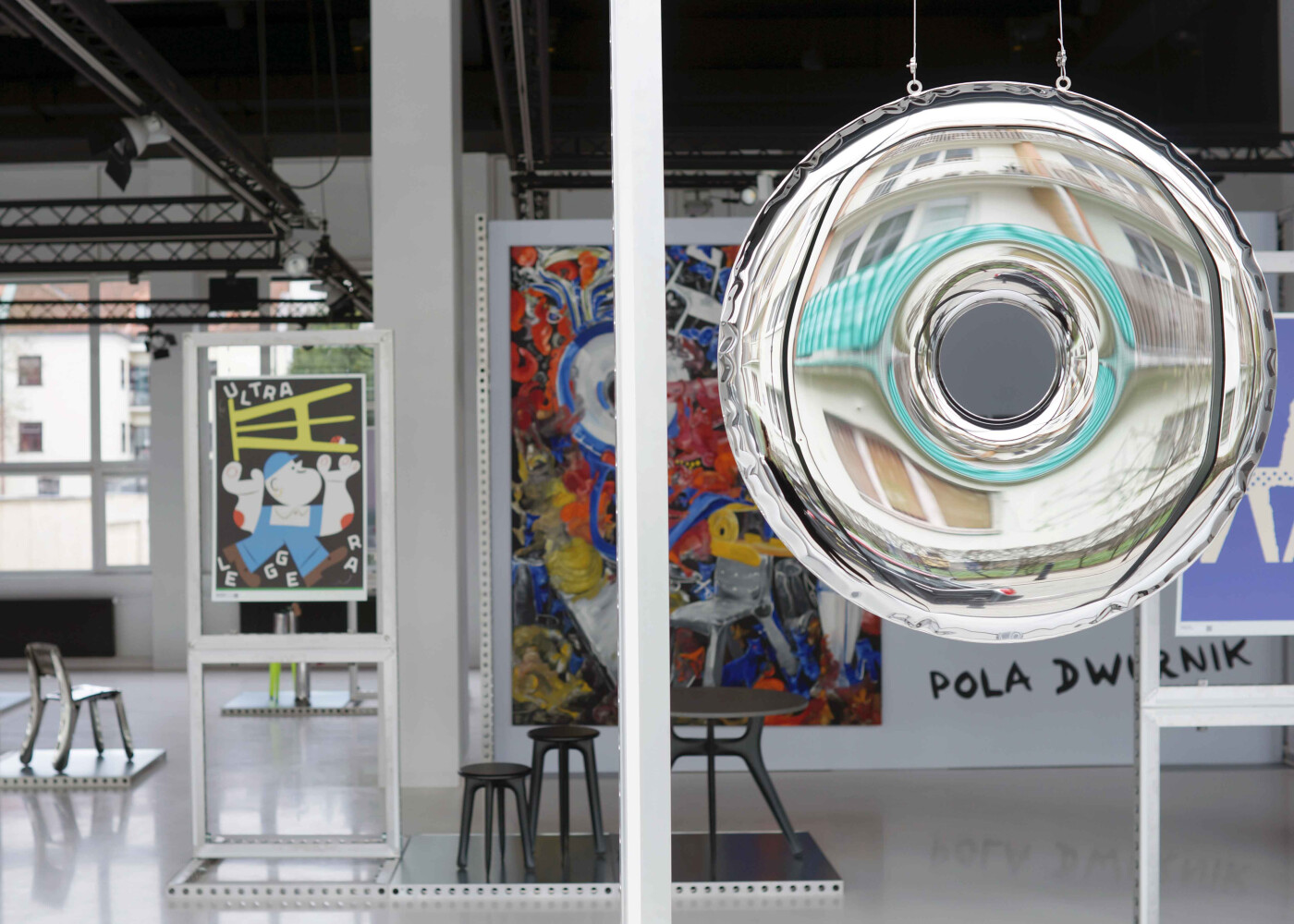
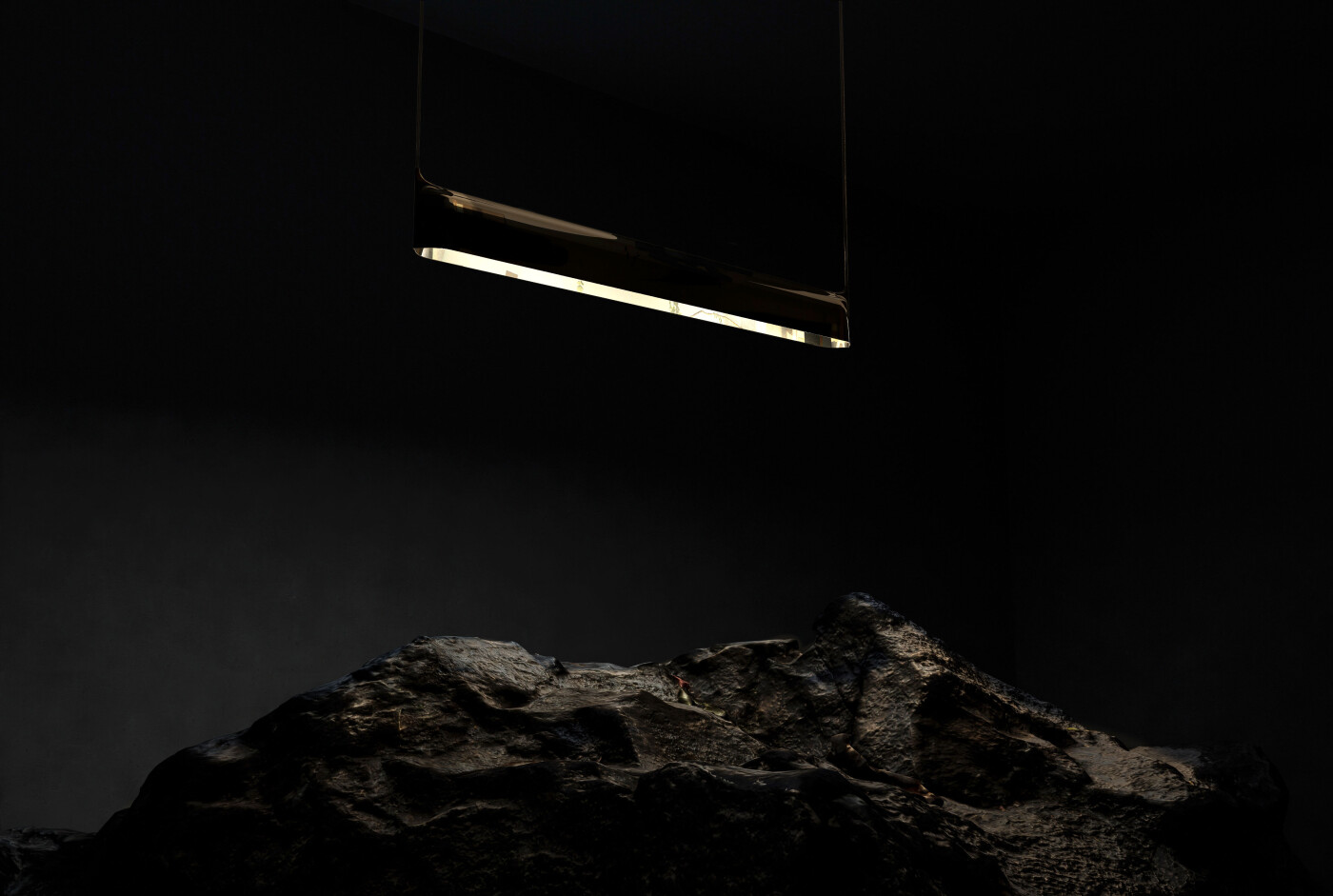
ABOUT LIGHT
Get into the magic of reflections
Explore collections
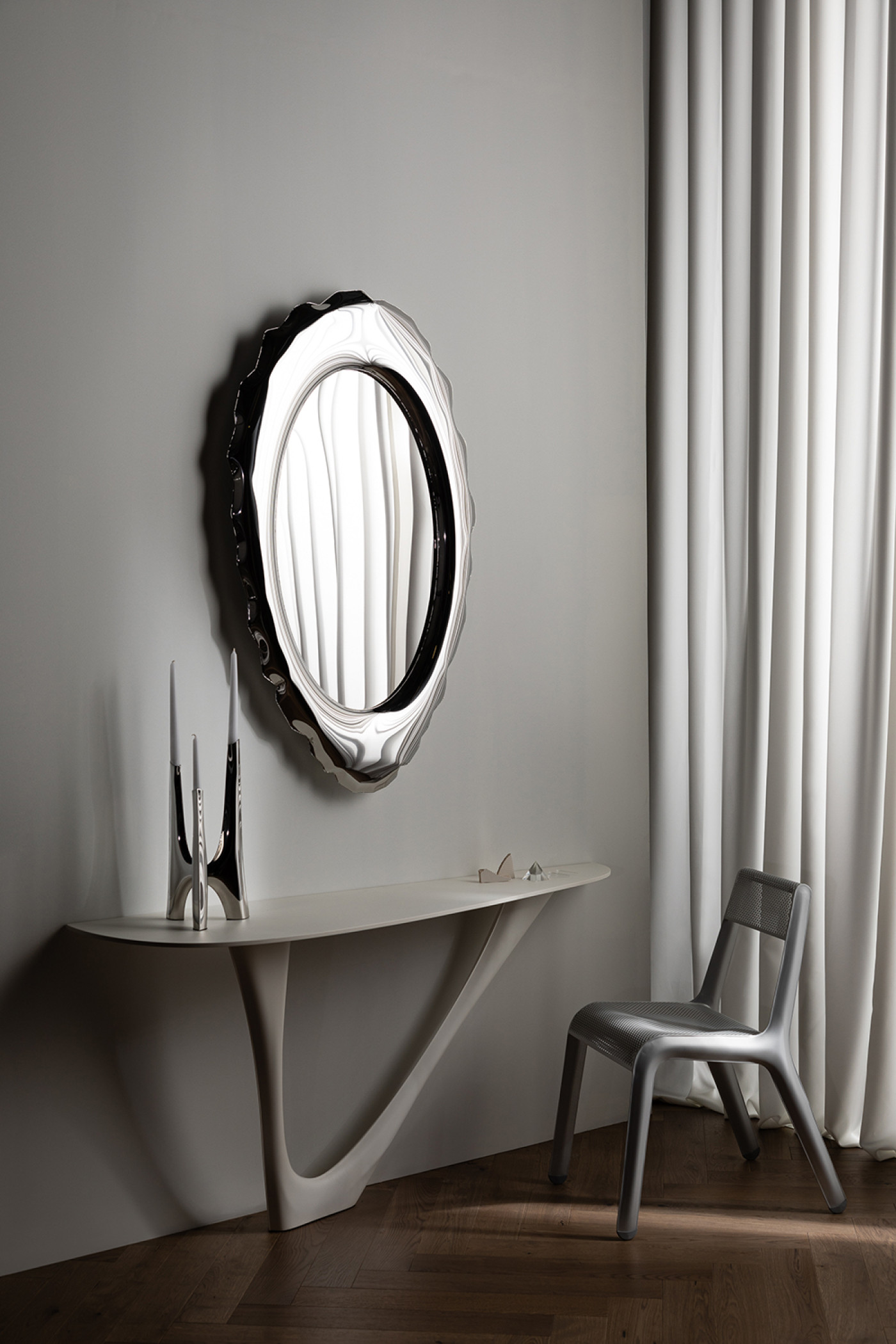
Zieta Collection
It’s an outcome of transdisciplinary design based on experimenting with the unique FiDU technology. Fresh, new and daring solutions that not only excite but also fire up the imagination.

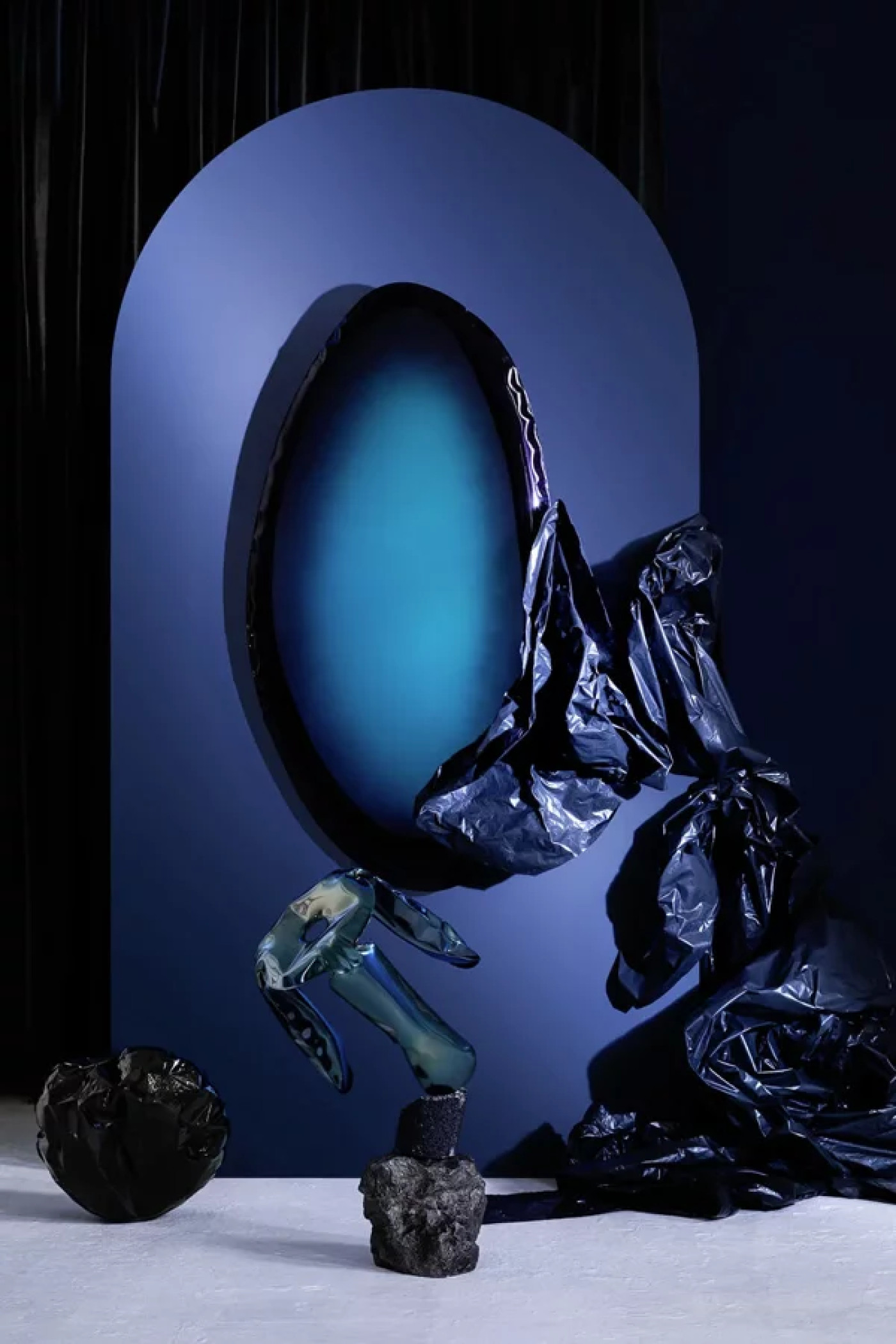
Gradient Collection
Mirrors from the Gradient series are made of stainless steel, polished to a mirror finish, and covered with a special lacquer, creating on their surface a unique composition of colours with exceptional depth and unparalleled reflections.
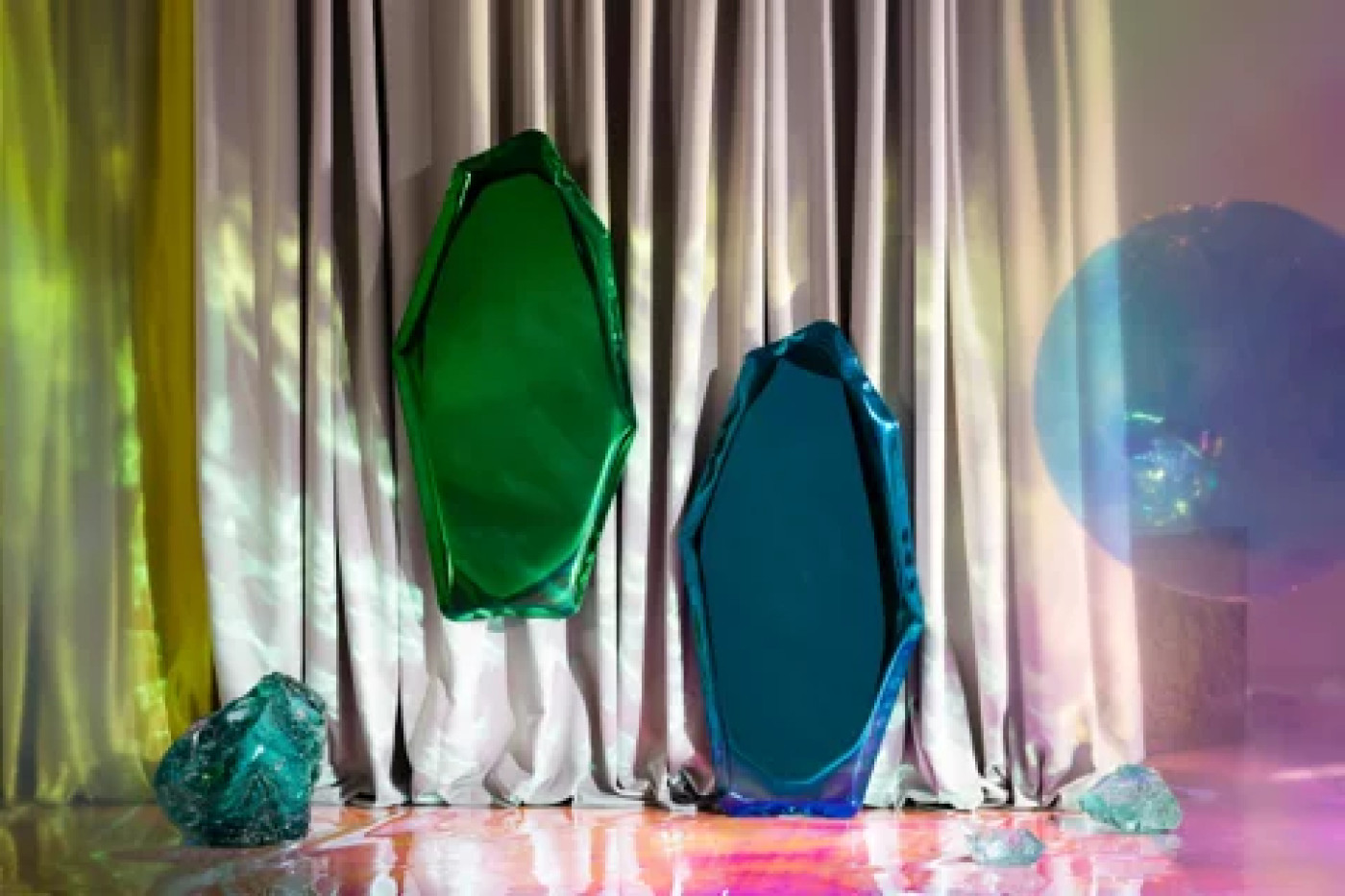

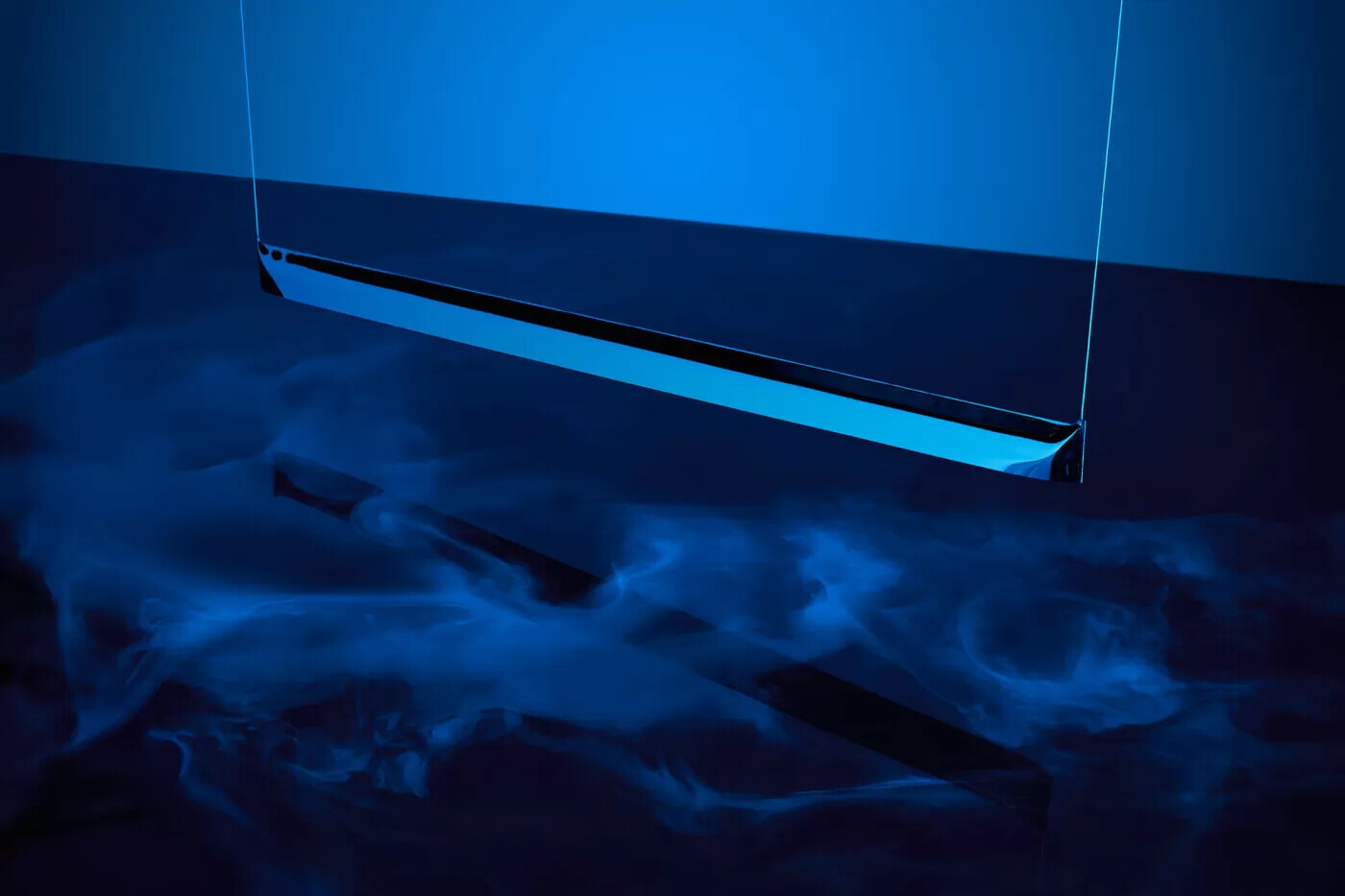
Zieta Lighting
Based on research, it is an adaptation of production to a demanding but sustainable future in the form of ambient, monomaterial lamps. It is the culmination of our admiration for light, reflections, and colours, through which we craft the art of illumination.
-large.jpg)
Latest projects
Sculptures
& other projects
Please select preferred language and currency to make ordering process easier for you.
It can be changed later in menu above
Confirm